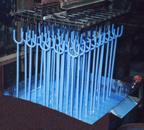
When we talk about our manufacturing processes we usually start at the beginning: sourcing the finest materials with an uncompromising concern for quality. It’s an open-ended effort, as we’re always looking out for new ways to improve.
Sometimes our efforts are in response to formal regulatory changes, like new medical device labeling requirements (see UDI Compliance: Ahead of the Curve). In other cases, we spot trends in the types of questions scientists and agencies are asking and initiate improvements on our own, anticipating that new rules are probably not too far behind.
More than a decade ago, for example, the Food and Drug Administration (FDA) and Centers for Disease Control (CDC) began studying phthalates, a group of chemicals used as binding agents and to make plastics more flexible. Phthalates are used in hundreds of products across several industries, including cosmetics, automobiles, and flooring. In the medical world, phthalates have been used in products like blood storage containers and tubing.
Our initial focus was on our stethoscope tubing. All of our Adscope and Proscope stethoscopes are made using a dip-molding process in which tubing molds are immersed repeatedly into liquefied, molten plastic polymer until they reach the specified thickness. (It costs more than other methods, like extruding, but we think it’s an important investment in quality.)
After a period of study and testing, we finalized a biodegradable, food-grade replacement for the phthalate plasticizer, one that’s compatible with our dip-molded production systems, and began using it in 2013. Initially, we converted our reusable Proscope instruments, with the Adscope line adapted in 2014. It’s a solution that has allowed us to eliminate the use of phthalates in this tubing – as well as the chestpiece rims and rings -- while retaining our signature softness, flexibility, and durability.
With that task complete, we turned our attention to the tubing in our blood pressure products. Testing has begun and we hope to move to non-phthalate production in 2017. If you have questions about this or any other aspect of our manufacturing process, please let us know.